Cutting bending drawing ε. A - 1 degree tolerance on all bend angles.
Ppt Chapter 10 Sheet Metal Design Powerpoint Presentation Free Download Id 6655822
Cutting and forming thin sheets of metal usually performed as cold working Sheet metal 04 164 to 6 mm 14in thick Plate stock 6 mm thick Advantage - High strength good dimensional accuracy good surface finish economical mass production low cost.
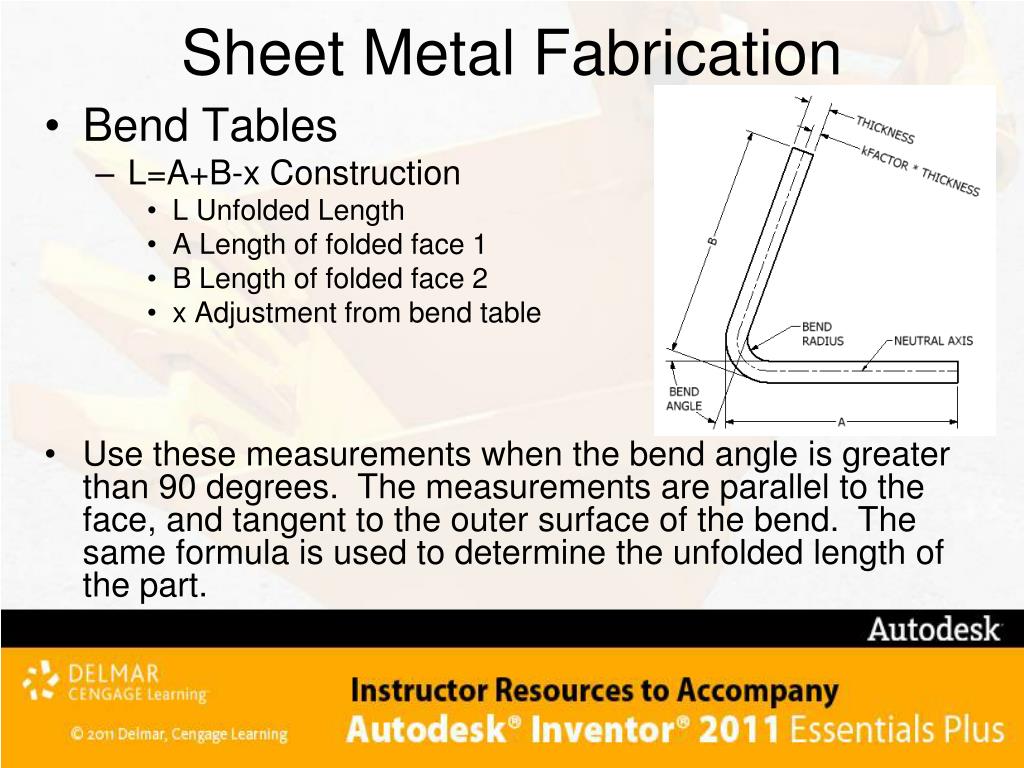
. In sheet metal forming practice we distinguish five basic modes of deformation. F YS UTS2 A. This mode is typical the material flow from the flange towards the.
Engineering changes can be costly. A minimum section must be one and one half times material thickness for high shear strength material for the most practical stamping. After completing this chapter you will be able to.
Usually made by hammering or rolling Trending Topics by Ak. Minimum Practical Section should never be less than material thickness or 060. Or how to put together simple things simply.
They have vast applications ranging from appliance industries automotive industries robotic industries and consumer products. Dies and Presses for Sheet Metal Processes 6. Plates thickness 6 mm inch.
O s Course outcomes CO1 Understand various general design rules for manufacture ability and criteria for material selection. Therefore it is essential to understand the basics of sheet metal design and the DFM sheet metal design guidelines considered in the manufacturing process. D 25T R see below The height can be less but it required secondary operations and is far more costly.
G India Business Center Part Design Guidelines Sheet Metal Part Design Guidelines. CO2 Apply various machining process and tolerance aspects in machining. Sheet Metal Bending Radius.
Sheet Metal Operations Not Performed on Presses 7. BASICS OF SHEET METAL USAGE OF NX- SHEET METAL TOOLS IN UNIGRAPHICS SHEET METAL. This article will help you to answer below interview questions in a better way.
Following are some basic sheet metal design Thump rules for Sheet metal Design. A great practice here is to ensure that the minimum bend radius for mild steel sheet metal is equal to its thickness. We will dive into the details of these techniques shortly.
M P Groover Fundamentals of Modern Manufacturing 3e SHEET METALWORKING 1. The PowerPoint PPT presentation. Outline Attaching things permanently and temporarily Simple structural supports and enclosures sealing o-rings Designing things that have to move bearings tracks jamming issues Modular solutions MK macrobench dexion Permanent Attachment Welding later Brazing later Rivets Glue Epoxy.
Work Features Holes Catalog Tools Mirror and Feature Patterns Promote. Stress distribution through the thickness of the part. It is difficult to follow all sheet metal design guidelines for complex sheet metal parts.
Learn practical sheet metal design with a strong theoretical understanding of underlying Design principles. F stretch forming force lbs YS material yield strength psi UTS ultimate tensile strength of the material psi A Cross-sectional area of the workpiece in2 Forces needed to bend sheet metal. Sheet metal parts with a minimum of 09mm to 20mm in thickness can be manufactured.
Sheet metal manufacturing is suitable for a range of metal materials. The most common sheet metal form is a bend. Sheet Metal Design 2018.
Sheets thickness 6 mm. A short summary of this paper. Other Sheet Metal Forming Operations 5.
Sheet metal involves work pieces with a high ratio of surface area to Thickness. If you design sheet metal parts you may know that bend relief is a notch cut made into the. Sheet Metal Fabrication - Sheet metal is a kind of integrated metal cold working technology for metal sheet usually in under 6mm usually the parts plastically deformed by handwork or stamping die to form your desired shape and size and it also can be further formed more complex parts by welding or other metal cold working technology including Laser cutting.
CO3 Analyze the design considerations for casting and welding process. Avoid large sheet metal parts with small bent flanges. Ppt on Sheet metal process 1.
Here is the list of best sheet metal design interview questions with their answers. These techniques often work in tandem with one another to produce the required part. The material is expanded in both directions.
The basic sheet metal fabrication techniques include cutting bending punching stamping welding and finishing. Bends can give strength and shape to a part and are formed in a machine using bend brakes. 2007 John Wiley Sons Inc.
Form height to thickness ratio To determine the minimum form height for sheet metal use the following formula. Bending in 4-slide machine Used for short pieces Controlled and synchronized with vertical die movements to form the part of desired shape. Chapter 10 Sheet Metal Design is.
Fig 1624 a Bead forming with a single die b Bead forming with two diesin a press brake. For the ease of manufacturing multiple bends on the same plane should occur in the same direction. The more flexible the metal the easier it is to attain a small inner bend radius.
Up to 10 cash back Added 4 Design projects - Mechanical Design of simple sheet metal brackets using Auto desk Fusion 360 for specific problem statements. Since sheet metal cannot be bent to a 90-degree position without breaking at sharp corners all bends will have an acceptable bend radius. When designing parts for laser cutting one should not make holes smaller than the thickness of the material.
-9- Stamping Basics Involve us during design stage to optimize cost and performance in component design. This course covers the essential basic theoretical and practical knowledge required for Designing Sheet. CO4 Apply the conceptual design factors to be considered in forging extrusion and sheet metal.
We follow Sheet metal design guidelines to ensure the quality and manufacturability of sheet metal enclosures. Read this article on sheet metal design guidelines before reading these questions and answers. Bends in the same plane should be designed in the same direction.
The minimum sheet metal bend radius depends on the manufacturing process and tool used. Bends in sheet metal are manufactured using sheet metal brakes. This mode of deformation is found mostly on smooth bottoms of shallow parts and in hydroforming processes.
When designing a sheet metal. Full PDF Package Download Full PDF Package. Sheet metal design guidelines.
The periphery if the sheet metal is bent into the cavity of a die. As a result you can deliver the product at a low cost and faster timeline. Sheet Metal Basics design guidelines a metal sheet varying in between 0154mm to 635mm.
Continuing our focus on sheet metal forming this issue of DFM guidebook focuses on design guidelines for bend relief parameters distance between holes and bends and offset bend material when a bend is made close to an edge. Sheet metals have an undeniable significance in our lives.
Chapter 10 Sheet Metal Design Ppt Download
Ppt Chapter 10 Sheet Metal Design Powerpoint Presentation Free Download Id 6655822
Chapter 10 Sheet Metal Design Ppt Download
Chapter 10 Sheet Metal Design Ppt Download
Sheet Metal Working Processes Ppt Download
Sheet Metal Working Processes Ppt Download
0 comments
Post a Comment